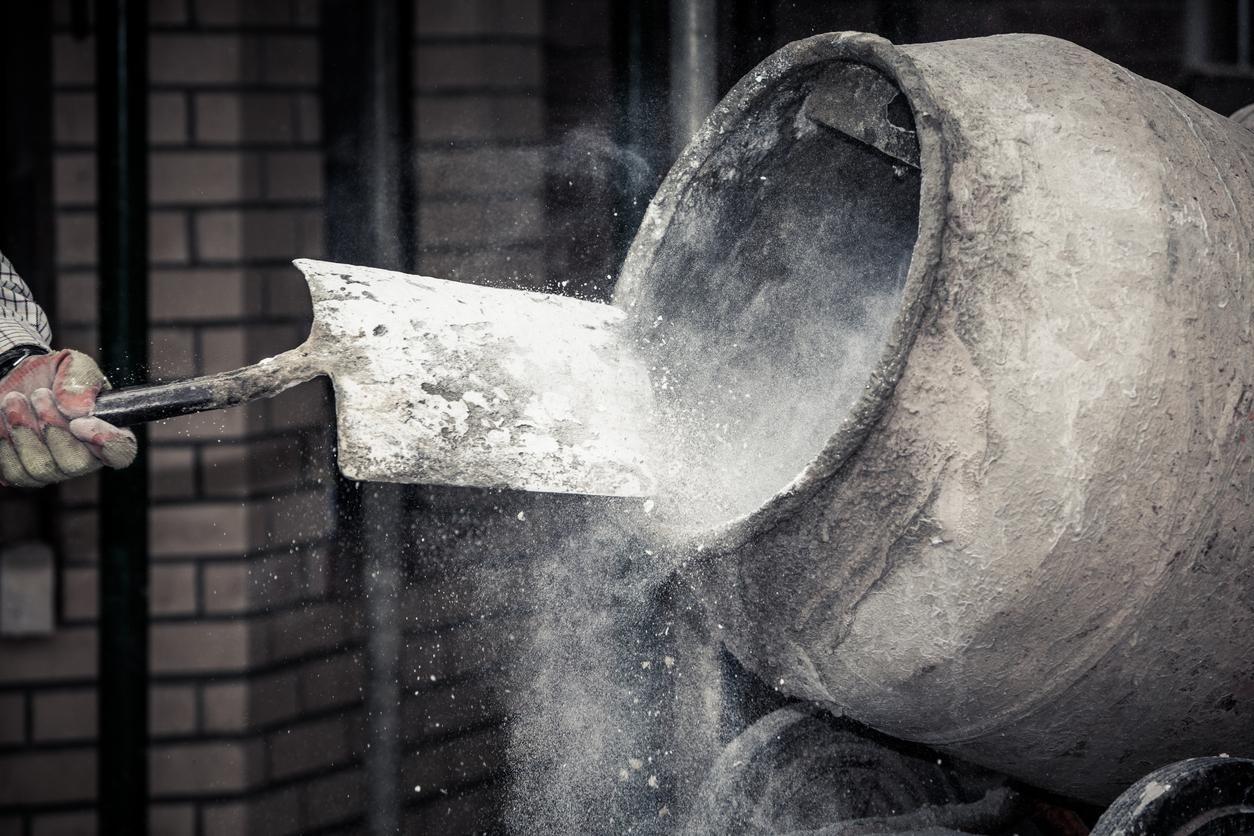
To say that cement is not environmentally friendly is an understatement. In fact, it is responsible for 7% of all carbon dioxide emissions—more than all the trucks on earth produce. Architects and designers focus on how much energy their buildings use, but it is the carbon footprint of the materials themselves that need attention. Cement manufacturers have already created greener alternatives, but they are finding end users slow to adopt their new products.
One of the reasons customers are balking at the new cement products is cost: “There is so far too little demand for sustainable materials,” Jens Diebold, head of sustainability at cement producer LafargeHolcim told Bloomberg. “I would love to see more demand from customers for it. There is limited sensitivity for carbon emissions in the construction of a building.”
It’s the chemical process used to manufacture cement that causes its high emissions footprint. During the manufacturing process, limestone is burnt in giant kilns that reach more than 1,400 degrees Celsius (2,600 degrees Fahrenheit). Carbon trapped in the limestone combines with oxygen to produce CO2.
According to the European Cement Association, manufacturing a ton of cement releases half a ton of CO2. A single cement mixer can carry around 13 tons.
The IEA estimates that production of cement will rise 12% to 23% by 2050 if action is not taken. Cement manufacturers have created alternatives using different production processes, but higher prices have led to very slow adoption by buyers. That cost barrier is not an insignificant one. Greener cement products can cost up to triple what traditional cement costs. Researches at the University of North Carolina at Charlotte discovered that a yard of geopolymer cement can cost as much as $161, while common Portland cement goes for $51.
The biggest issue with cement is clinker. This is the substance that comes out of the kiln where limestone is burned. It is mixed with water and gypsum and binds with gravel to form concrete. Cutting the amount of clinker would reduce the environmental impact of cement products.
Some manufacturers are looking at clinker alternatives like fly-ash (a by-product of burning coal) and slag from furnaces in steel manufacturing. Cement using these two alternatives is called geopolymer cement and is far more sustainable. Obtaining these by-products can be difficult in some countries.
“This alternative eco-friendly binder technology reduces the carbon emissions associated with normal Portland cement by 80% to 90%, and also has a much lower embodied energy,” Cameron Coleman, chief executive officer of Wagners Holding Co. “We have been working with leading companies in South East Asia, New Zealand, India, Europe and the Middle East who are extremely interested in adopting this technology.”
Another alternative is pozzolan, a siliceous and aluminous material that is popular in Brazil. The adoption of this alternative is so widespread that Brazil’s clinker content was below 70% in 2014, the lowest in the wold. Brazil hopes to reduce that to 50% by 2050. With coal plants closing at a rapid rate, Europe and the US (who both rely on fly-ash) are struggling to find alternatives.
With carbon allowances tightening the world over, cement manufacturers are under increasing pressure to reduce emissions. Unless governments move to legislate cement use, buyers are unlikely to opt for greener alternatives for fear of impacting their bottom lines.