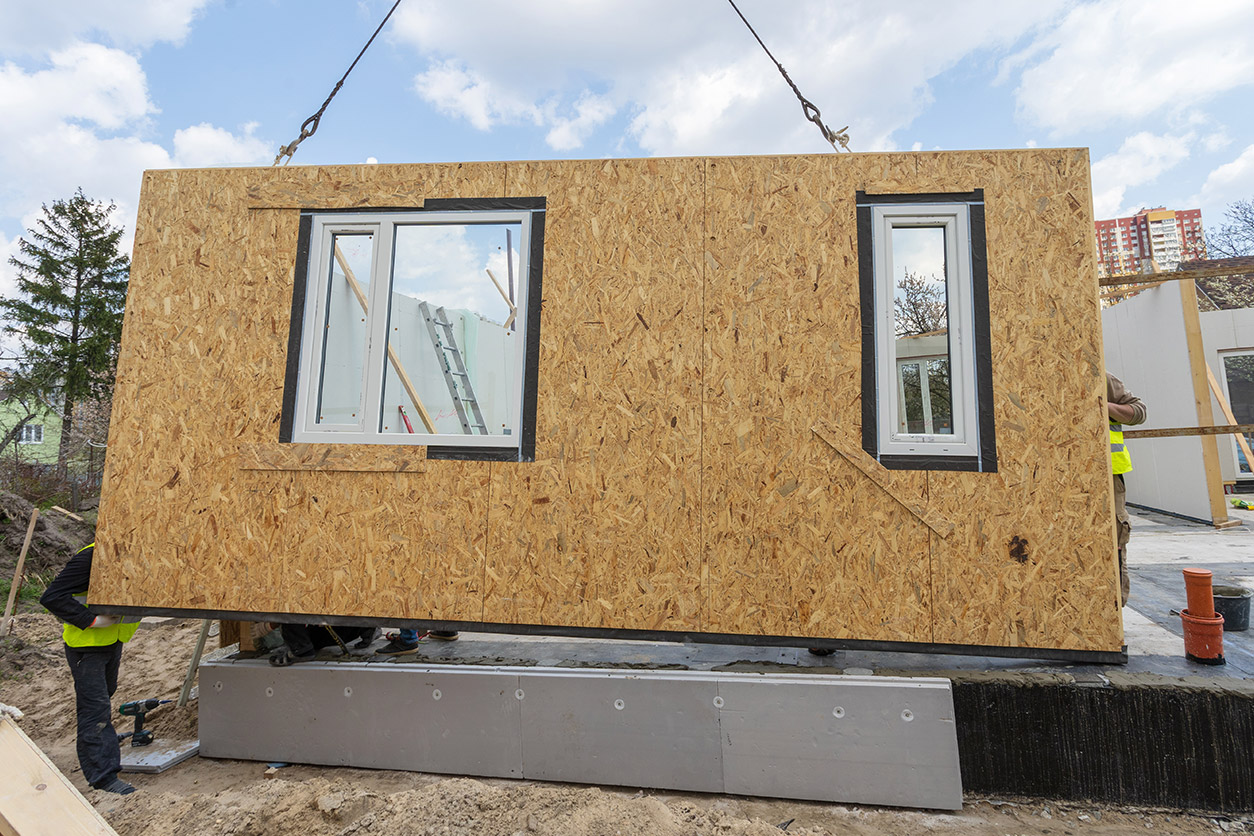
Prefab construction is not a new idea, but it’s not been a particularly successful one in the past. This time around, Katerra is finally getting it right. One of the best examples of this is the Katerra K90 Building Project which notes: “some 70 percent of construction projects come in overtime and over budget” and that onsite building is “cumbersome, inefficient, and no longer viable in the face of growing demand for housing… Katerra is working to change this, applying methods and tools such as digital technology, offsite manufacturing, and fully-integrated teams in an effort to improve construction productivity.”
Katerra’s innovative approach comes at a time when significant labor shortages are exacerbating delays and significantly increasing the cost of building. With their K90 project. Katerra showed how an apartment complex could be built in 90 days instead of 140 with less waste and a better quality build.
“When a manufacturing facility wants to build a complex machine – take an automobile – engineers representing different disciplines study each piece individually and iterate on their design to create a more perfect answer that is designed with actual fabrication in mind,” Katerra writes. “This is how each deliverable was taken apart and pieced back together in the most optimized way possible. Then, using an integrated schedule, deliverables are viewed as a whole; instead of each piece being managed in an independent silo, components are planned with very granular details and managed like pieces of a bigger puzzle.”
Each component of the building is manufactured in factory conditions which ensures greater accuracy and less waste. Components get an RFID tracking number so construction managers are able to track each component from factory floor to building site. That means builders can predict the arrival of components down to the hour so they can prepare the site and seamlessly orchestrate a faster assembly.
Building designs are ‘products’ so by productizing building components, costs are reduced and components can be easily replicated. This is the perfect answer to the housing shortage. Katerra has a library of building types and sizes that fit regional building codes. That means clients can choose standard building models but tailor finishes to their own needs and tastes.
For example, the bathroom component comes complete with toilet, vanity, flooring and plumbing and electrical fixtures. The bathroom pod just has to be placed and hooked up. That means the K90 project saw all bathrooms installed in less than one working day by two people.
Here’s a look at some other stats from the K90 project:
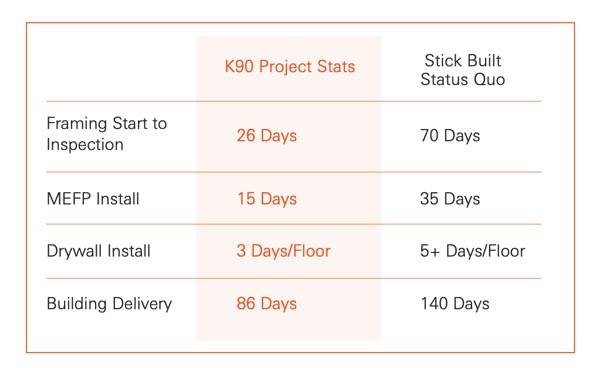
Image by Katerra
With their approach to building, Katerra is providing real solutions to construction labor shortages and filling a niche in the mass housing market that needs urgent attention.